"이 포스팅은 쿠팡 파트너스 활동의 일환으로, 이에 따른 일정액의 수수료를 제공받습니다."
서론
그라비아 인쇄는 고해상도와 깊이 있는 색상 표현 능력으로 인해 다양한 산업 분야에서 선호되는 인쇄 방식입니다. 그러나 이러한 방식은 복잡하고 정밀한 기술을 요구하며, 각 과정이 밀접하게 연관되어 있습니다. 이 글에서는 그라비아 인쇄의 각 단계를 깊이 있게 분석하고, 그 과정에서 중요한 요소들을 살펴보겠습니다. 또한, 그라비아 인쇄가 가지고 있는 환경적 문제와 이를 해결하기 위한 가능한 방안에 대해서도 논의하겠습니다. 이를 통해 그라비아 인쇄의 현 상황과 향후 발전 방향에 대한 이해를 돕고자 합니다.
플렉소와의 차이, 그리고 대략적인 정리는 아래 글을 참고해주시길 바랍니다.
https://10yp.tistory.com/51
포장지 인쇄 방법 - 그라비아 인쇄, 플렉소 인쇄
서론 식품 포장지 인쇄 방식은 제품의 품질과 브랜드 이미지, 또한 식품의 안전성에도 큰 영향을 미치는 요소입니다. 특히 그라비아 인쇄와 플렉소 인쇄는 식품 포장지 인쇄에서 가장 일반적으
10yp.tistory.com
플렉소 인쇄에 대한 내용은 아래 글을 참고해주시길 바랍니다.
https://10yp.tistory.com/113
플렉소 인쇄(Flexo Printing) 이해하기
서론 플렉소 인쇄는 그 높은 유연성과 다양한 재료에 대한 호환성으로 인해 널리 사용되는 인쇄 기법 중 하나입니다. 이 기법은 플라스틱, 금속, 종이 등 다양한 재료의 인쇄에 적합하며, 특히
10yp.tistory.com
절차
1. 동판 제작
인쇄물의 품질은 동판 제작 과정에서 크게 결정됩니다. 디자인은 컴퓨터로 제작되며, 이후 레이저 혹은 헤리오를 통해 동판에 각인됩니다. 이 때 각인 깊이는 인쇄물의 색상 진하기를 결정짓게 되며, 이는 각 색상의 잉크 흡수량을 조절하는 역할을 합니다. 이 과정에서는 높은 정밀도가 요구되며, 레이저 기술의 발전에 따라 그 정밀도는 더욱 향상되고 있습니다.
동판의 선수와 심도
동판의 제판 시 선수와 심도를 조정하여 도포량을 조절할 수 있습니다. 선수는 기준 길이 안에 들어가는 선의 개수를 나타내며, 이는 인쇄의 해상도 즉, 선명도를 나타내는 중요한 지표입니다.
예를 들어, '200선'은 1인치에 200개의 선이 각인된 것을 의미하며, 이는 고해상도 인쇄를 나타냅니다. 반면 '175선'은 1인치에 175개의 선이 각인된 것으로, 이는 상대적으로 낮은 해상도를 나타냅니다.
따라서 이 숫자가 클수록 세밀한 인쇄가 가능하며, 이미지의 세부 사항을 더욱 잘 재현할 수 있습니다. 하지만, 선 스크린이 높을수록 인쇄 과정이 복잡해지고 비용이 상승하는 경향이 있습니다.
심도는 동판에 각인된 선의 깊이를 의미합니다. 심도가 깊으면 잉크의 흡수량이 많아져 색상이 진해지고, 심도가 얕으면 잉크의 흡수량이 적어져 색상이 연해집니다. 심도는 또한 잉크가 동판에 얼마나 오래 머무르는지를 결정하므로, 인쇄 과정에서 잉크가 동판에 부착되는 시간을 조절하는 역할을 합니다.
헤리오 제판과 레이저 제판
그라비아 인쇄에서 사용되는 두 주요 제판 방법인 레이저 제판과 헤리오 제판은 각기 다른 기술을 사용하여 동판에 이미지를 각인합니다. 이들은 각각의 장단점을 가지고 있으며, 이를 이해하는 것은 인쇄물의 품질과 비용, 그리고 제작 시간을 결정하는 중요한 요소입니다.
레이저 제판은 현대적인 방식으로, 컴퓨터를 이용해 디자인을 작성한 후, 레이저를 사용해 동판에 이미지를 각인합니다. 이 방식은 고도의 정밀성과 빠른 속도를 가지며, 복잡한 디자인과 세밀한 그래픽을 빠르게 그리는 데 효과적입니다. 또한, 물리적인 접촉 없이 동판을 각인하기 때문에 동판의 손상 위험이 적습니다. 그러나, 레이저 제판기는 초기 투자 비용이 크며, 유지 보수가 필요한 경향이 있습니다.
헤리오 제판: 헤리오 제판은 그라비아 인쇄의 전통적인 방식으로, 다이아몬드 스타일러스를 이용해 동판에 이미지를 각인합니다. 스타일러스는 동판의 표면을 미세하게 파서 이미지를 형성하며, 이 과정은 세밀한 디테일과 깊이 있는 색상 표현이 가능하다는 장점이 있습니다. 그러나, 이 방식은 높은 기술적 요구사항과 시간이 많이 소요되는 단점이 있습니다. 헤리오 제판은 주로 고급 인쇄물이나 대량 인쇄에 사용되는 경향이 있습니다.
따라서, 레이저 제판과 헤리오 제판은 각각의 장단점에 따라 적절한 상황과 요구 사항에 따라 선택되어야 합니다. 레이저 제판은 빠른 속도와 고해상도가 필요한 경우에 적합하며, 헤리오 제판은 세밀한 디테일과 깊이 있는 색상 표현이 중요한 고급 인쇄물에 적합합니다.
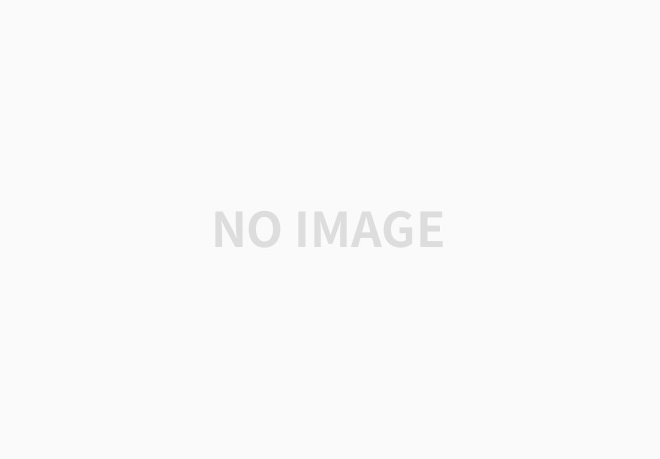
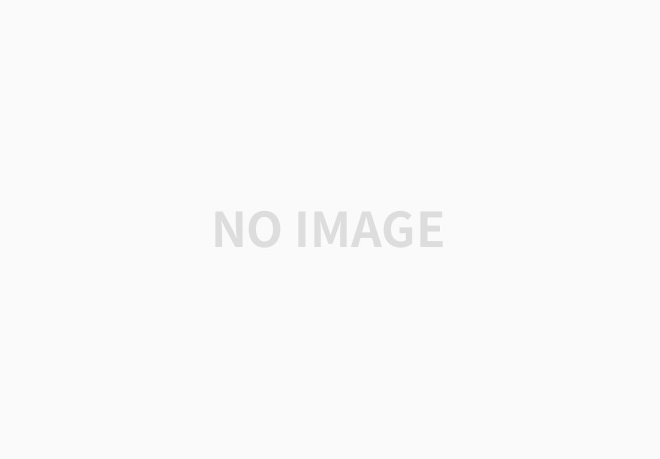
2. 크롬 도금
동판 제작 후에는 크롬 도금 과정이 이루어집니다. 이는 동판의 표면을 보호하고 잉크의 부착력을 높이는 역할을 합니다. 크롬 도금으로 인해 동판 표면에 미세한 홈이 형성되며, 이 홈에 잉크가 더 잘 부착되어 인쇄 품질이 향상됩니다.
3. 잉크 도포
잉크 도포 과정에서는 동판에 적절한 양의 잉크가 도포됩니다. 이 과정에서 잉크의 두께와 분포는 인쇄물의 색상 표현과 해상도에 큰 영향을 미치게 됩니다. 잉크는 동판의 각인된 부분에만 채워지며, 이를 위해 동판이 회전하면서 잉크 트레이에 닿게 됩니다.
그라비아 인쇄 과정에서 잉크 도포는 중요한 단계로, 이 때는 다양한 요소들을 고려해야 합니다. 특히, 잉크의 수지 구성, 용제 구성, 동판 및 필름과의 전이성 등이 크게 영향을 미치게 됩니다.
4. 잉크 스크래핑
잉크 도포 후에는 Doctor Blade라는 도구를 사용해 동판 표면의 잉크를 제거합니다. 이는 각인되지 않은 부분에서 잉크를 제거하고, 각인된 부분에만 잉크가 남도록 하는 과정입니다. 이렇게 해서 인쇄될 이미지의 선명도가 높아집니다.
이 때 독타날(Doctor Blade)의 적절한 압력 조정이 필요하며, 독타날이 마모될 경우 마모된 부위에서 각인되지 않은 부분에도 인쇄가 될 수 있습니다. 이것을 일반적으로 독타줄이라고 표현합니다. 독타날의 한 부위가 마모되어 줄이 아닌 면의 형태로 넓게 나타날 경우도 있으며, 이것은 일반적으로 독타날의 양쪽 압력이 고르지 못할 경우에도 생깁니다.
5. 인쇄
잉크가 적용된 동판은 종이와 빠르게 접촉하며 인쇄 이미지를 전달합니다. 이 때 동판은 종이에 대해 매우 높은 압력을 가하므로, 잉크가 종이에 깊게 침투하고 고르게 퍼지게 됩니다.
이 때 잉크 구성과 용제 구성, 그리고 그 조합에 의해 인쇄성이 결정됩니다.
잉크의 수지는 잉크의 점도와 건조 속도를 결정짓는 중요한 요소입니다. 수지의 선택은 인쇄 속도, 인쇄물의 품질, 그리고 인쇄 과정에서의 잉크의 건조 속도 등에 큰 영향을 미칩니다. 따라서 잉크의 수지 구성은 인쇄 과정의 효율성과 인쇄물의 최종 품질에 중요한 역할을 합니다.
용제는 잉크의 점도를 조절하고 건조 속도를 관리하는 역할을 합니다. 용제의 선택은 잉크가 동판에서 필름으로 잘 전이되는지, 그리고 잉크가 필름에 얼마나 빨리 건조되는지 등에 영향을 미칩니다. 따라서 용제의 구성은 인쇄 과정의 효율성과 인쇄물의 최종 품질을 결정짓는 중요한 요소입니다.
잉크의 전이성은 잉크가 동판에서 필름으로 얼마나 잘 전달되는지를 나타냅니다. 잉크의 전이성은 잉크의 수지 구성, 용제 구성, 그리고 동판의 표면 처리 등에 의해 결정됩니다. 잉크의 전이성이 좋아야 선명도가 높은 인쇄물을 얻을 수 있으며, 이는 인쇄 과정의 효율성과 인쇄물의 최종 품질을 결정하는 중요한 요소입니다. 이처럼 잉크 도포 과정에서는 다양한 요소들을 고려해야 합니다. 이 요소들은 각각 인쇄 과정의 효율성과 인쇄물의 최종 품질에 큰 영향을 미치므로, 인쇄물의 요구 사항과 인쇄 환경에 따라 적절히 조절되어야 합니다.
6. 권취
마지막으로, 인쇄물은 각 동판 위에 설치된 건조 챔버를 통과하여 잉크가 완전히 건조되도록 합니다. 이 과정에서 용제가 증발하며, 이후에 인쇄물은 권취되어 완성됩니다. 권취 시에는 텐션과 테이퍼가 중요합니다.
텐션
필름이나 종이 등의 인쇄 물질에 가해지는 힘을 의미합니다. 적절한 텐션은 인쇄 물질의 안정성을 유지하고, 인쇄 과정 중에 발생할 수 있는 문제점을 방지하는 데 중요합니다. 텐션이 너무 높으면 필름이 찢어지거나 변형될 수 있으며, 텐션이 너무 낮으면 필름이 제대로 움직이지 않아 인쇄 과정이 방해될 수 있습니다. 따라서 적절한 텐션을 유지하는 것은 인쇄 과정의 효율성과 인쇄물의 품질을 결정짓는 중요한 요소입니다.
테이퍼
테이퍼는 필름이나 종이 등의 인쇄 물질의 두께가 점차적으로 변하는 것을 의미합니다. 적절한 테이퍼는 인쇄 물질의 안정성을 높이고, 인쇄 과정 중에 발생할 수 있는 문제점을 방지하는 데 중요합니다. 테이퍼가 너무 높으면 필름의 두께가 너무 빠르게 변해 인쇄물의 품질이 떨어질 수 있으며, 테이퍼가 너무 낮으면 필름의 두께 변화가 충분하지 않아 인쇄 과정이 방해될 수 있습니다. 따라서 적절한 테이퍼를 유지하는 것은 인쇄 과정의 효율성과 인쇄물의 품질을 결정짓는 중요한 요소입니다.
이처럼, 권취 과정에서는 텐션과 테이퍼를 적절히 조절해야 합니다. 이 두 가지 요소는 인쇄 과정의 효율성과 인쇄물의 최종 품질에 큰 영향을 미치므로, 인쇄물의 요구 사항과 인쇄 환경에 따라 적절히 조절되어야 합니다.
이렇게 그라비아 인쇄는 깊이 있는 색상 표현과 높은 해상도를 위해 여러 단계의 복잡한 과정을 거쳐 진행됩니다. 그러나 이 모든 과정은 고도의 기술과 경험을 필요로 하며, 각 단계가 서로 밀접하게 연관되어 있어 과정 하나하나가 인쇄물의 최종 품질에 결정적인 영향을 끼칩니다.
그라비아 인쇄의 한계와 발전 방향
그라비아 인쇄는 뛰어난 선명도와 채도, 그리고 높은 인쇄 품질로 인해 많은 인쇄 산업에서 선호되는 인쇄 방식입니다. 그라비아 인쇄는 깊이 있는 각인을 통해 잉크를 도포하기 때문에 잉크 도포량이 많으며, 이로 인해 높은 색상의 진하기와 더 나은 이미지 품질을 제공할 수 있습니다.
그러나, 그라비아 인쇄는 그 많은 장점에도 불구하고 몇 가지 단점이 존재합니다. 그 중 가장 큰 것이 바로 환경에 미치는 영향입니다. 그라비아 인쇄는 대량 생산을 위한 인쇄 방식이기 때문에 인쇄 공정 중에 발생하는 폐기물과 화학 물질의 사용이 환경에 부정적인 영향을 미칠 수 있습니다. 또한, 그라비아 인쇄에 사용되는 잉크에는 인체에 유해한 화학 물질이 포함되어 있을 수 있습니다. 이는 식품 안전성에 직접적인 위협이 될 수 있습니다.
이러한 이유로, 그라비아 인쇄는 환경적 측면에서 많은 문제를 야기하며, 이에 대한 해결책을 찾는 것이 필요합니다. 환경 친화적인 그라비아 인쇄 방법의 개발 환경 친화적인 그라비아 인쇄 방법의 개발은 인쇄 산업에서 중요한 이슈입니다. 그라비아 인쇄의 환경 문제를 해결하기 위한 방법 중 하나는 바로 물 기반 잉크의 사용입니다. 물 기반 잉크는 용매 기반 잉크보다 더 적은 화학 물질을 사용하므로, 환경에 더 적은 영향을 미칩니다.
또한, 물 기반 잉크는 인체에 미치는 영향도 적습니다. 그러나, 물 기반 잉크를 사용하는 것이 환경 문제를 완전히 해결하는 것은 아닙니다. 물 기반 잉크를 사용하더라도, 그라비아 인쇄 공정 중에는 여전히 폐기물이 발생합니다. 따라서, 그라비아 인쇄 공정 자체를 보다 환경 친화적으로 개선하는 방법이 필요합니다. 이를 위해, 인쇄 판의 재활용이나, 인쇄 공정에서 발생하는 폐기물을 최소화하는 기술의 개발이 중요합니다. 또한, 에너지 효율을 높이는 기술도 그라비아 인쇄의 환경 문제를 해결하는 데 기여할 수 있습니다.
결론
그라비아 인쇄는 높은 인쇄 품질과 광범위한 색상 표현력으로 인해 많은 인쇄 산업에서 선호되는 인쇄 방식입니다. 그러나, 그라비아 인쇄는 그 많은 장점에도 불구하고 환경에 미치는 부정적인 영향과 식품 안전성에 대한 문제를 안고 있습니다. 이러한 문제를 해결하기 위해, 환경 친화적인 그라비아 인쇄 방법의 개발이 필요합니다. 이는 물 기반 잉크의 사용, 인쇄 판의 재활용, 인쇄 공정에서 발생하는 폐기물의 최소화, 에너지 효율의 향상 등을 통해 이루어질 수 있습니다. 이렇게 환경 친화적인 그라비아 인쇄 방법의 개발은 인쇄 산업의 미래적인 방향을 제시하는 중요한 부분이라 할 수 있습니다.
함께 읽으면 좋은 글 ↓
플렉소 인쇄 Flexo Printing 이해하기
서론 플렉소 인쇄는 그 높은 유연성과 다양한 재료에 대한 호환성으로 인해 널리 사용되는 인쇄 기법 중 하나입니다. 이 기법은 플라스틱, 금속, 종이 등 다양한 재료의 인쇄에 적합하며, 특히
10yp.tistory.com
식품 포장 표면 처리 기술에 대하여 Corona treatment
서론 인쇄와 합지에 있어서 필름의 표면 처리는 핵심적인 요소입니다. 특히 플라스틱 필름의 경우, 표면 에너지를 높이는 코로나 처리가 널리 사용되고 있습니다. 그러나 코로나 처리는 그 과
10yp.tistory.com
식품은 어떻게 포장될까?
서론 식품의 포장은 앞서 살펴본 글들을 통해 중요성을 알 수 있습니다. 그렇다면 식품은 어떻게 포장될까요? 오늘은 식품 포장이 일어나는데까지의 여정을 함께해보겠습니다. 식품 포장은 그
10yp.tistory.com
https://10yp.tistory.com/entry/%EC%A2%85%EC%9D%B4-%EC%B9%9C%ED%99%98%EA%B2%BD
종이 = 친환경?
서론 지속 가능성이 선택이 아닌 필수가 된 시대에 우리가 일상에서 사용하는 재료들은 환경적 영향에 대한 면밀한 검토를 필요로 합니다. 여러 논란의 중심에 있는 종이 포장재는 지속 가능한
10yp.tistory.com
블로그 인기글
그라비아 인쇄(Gravure Printing) 이해 하기
서론 그라비아 인쇄는 고해상도와 깊이 있는 색상 표현 능력으로 인해 다양한 산업 분야에서 선호되는 인쇄 방식입니다. 그러나 이러한 방식은 복잡하고 정밀한 기술을 요구하며, 각 과정이 밀접하게 연관되어 있습니다. 이 글에서는 그라비아 인쇄의 각 단계를 깊이 있게 분석하고, 그 과정에서 중요한 요소들을 살펴보겠습니다. 또한, 그라비아 인쇄가 가지고 있는 환경적 문제와 이를 해결하기 위한 가능한 방안에 대해서도 논의하겠습니다. 이를 통해 그라비아 인쇄의 현 상황과 향후 발전 방향에 대한 이해를 돕고자 합니다. 플렉소와의 차이, 그리고 대략적인 정리는 아래 글을 참고해주시길 바랍니다. https://10yp.tistory.com/51 포장지 인쇄 방법 - 그라비아 인쇄, 플렉소 인쇄서론 식품 포장지 인쇄 방식은..
10yp.tistory.com
DSC의 원리와 이해
서론 최근 환경 친화적이고 안전한 식품 포장 소재 개발에 대한 요구가 높아지고 있습니다. 이러한 배경 속에서, 고분자 물질인 PE(Polyethylene), PP(Polypropylene), NY(Nylon), PET(Polyethylene Terephthalate) 등이 식품 포장용 필름으로 널리 사용되고 있습니다. 이들 소재는 각각의 독특한 물리적, 화학적 특성을 가지며, 이는 식품의 신선도 유지, 보관, 운송 등 다양한 측면에서 중요한 역할을 합니다. 이러한 고분자 물질들의 특성을 이해하고 분석하는 데에는 다양한 방법이 있지만, 특히 DSC(Differential Scanning Calorimetry) 방법이 유용하게 사용됩니다. DSC는 물질의 열 특성을 분석하는 실험 기법으로, 물질이 가열되거..
10yp.tistory.com
'식품 포장' 카테고리의 다른 글
스티로폼 박스와 그 대체제에 대한 비교 논문 리뷰 (3) | 2024.01.24 |
---|---|
플렉소 인쇄 Flexo Printing 이해하기 (4) | 2024.01.22 |
플라스틱 반찬통 용기 재사용해도 될까요? (4) | 2024.01.15 |
식품의 선도 유지제 (50) | 2024.01.04 |
식품 포장 표면 처리 기술에 대하여 Corona treatment (47) | 2023.12.29 |